Using RFID technology to optimize the mould management, the core lies in the digital identification, automated data collection and intelligent system linkage, to solve the traditional management of the efficiency, precision and cost pain points. The following is the specific implementation path and key strategies:
Establishment of the mould ‘digital identity’: from physical to digital unique identification
Industrial grade tag selection
For the mould metal material and complex working conditions, the choice of metal-resistant RFID tags to support – 40 ℃ ~ 200 ℃ temperature resistance, IP68 waterproof and dustproof, to ensure stable work in the stamping, injection moulding, heat treatment The tag integrates the basic information of the mould (Модели, type and location).
The tag integrates the basic information of the mould (Модели, материал, production batch), writes the unique ID through the special reader, and binds with PLM/MES system, forming the digital twin foundation of ‘one mould, one file’.
Full life cycle identification covers
sticking labels on the mould body (Например. mould frame, cavity), removable parts (Например. ejector pins, springs) to achieve full chain tracking from assembly, use to scrap, solving the problem of ‘difficult to trace the replacement of parts’ in traditional management.
Automated data collection: eliminate the efficiency bottleneck of manual intervention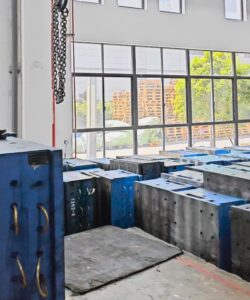
Real-time data capture of the whole scene
- Входящий и исходящий менеджмент: deploy door readers in the warehouse door/shelf, automatically identify the moulds in and out of the batch (читать 200+ labels in a single pass), complete the 5,000 pieces of moulds inventory in a minute, and the accuracy of inventory is increased from 85% Кому 99.9%, which solves the problem of ‘difficult to find the moulds’. ‘Difficulty in finding moulds’ and the problem of inventory backlog.
- Workstation data linkage: Fixed readers are installed in equipment workstations, automatically triggering identification when moulds are installed, and linking the PLC/CNC system to load matching process parameters (Например, давление, Температура), avoiding manual input errors, and shortening the time for mould changeover and adjustment of machines by 40%.
Closed-loop data for the whole process
During the production process, the reader collects real-time data such as mould usage hours, processing times, load pressure, и т.д., and automatically uploads them to the MES system to generate dynamic usage profiles. After the application in an auto parts factory, the omission rate is reduced from 30% Кому 1%, providing an accurate basis for maintenance decision-making.
Intelligent management and decision-making: from ‘after the fact’ to ‘before the fact’
Error prevention and compliance management
- Process error prevention: through the reader to verify the matching of moulds, equipment and materials (such as aluminium alloy moulds are prohibited for magnesium alloy processing), triggering audible and visual alarm and locking the equipment. The equipment is triggered by an audible and visual alarm and locked. В результате, a die-casting plant reduced 70% of the scrap caused by misuse of moulds.
- Compliance traceability: In aerospace and other areas with high compliance requirements, RFID records the time and operator of each maintenance and calibration of the mould to meet the traceability requirements of standards such as IATF 16949, increasing audit efficiency by 80%.
Predictive Maintenance Optimization
Based on the cumulative usage data collected by RFID (such as the number of times the mould is opened and closed, vibration amplitude), combined with machine learning algorithms to build a mould health model, it warns of component fatigue (such as wear of the guide pillar and aging of the seals) 3 Кому 5 days in advance, and automatically generates maintenance work orders.
The whole chain synergy: to open up the ‘man – машина – материал – method’ of the information silo
Inventory and logistics automation
- Intelligent warehousing: AGV robots read mould labels, automatically complete the handling from the elevated library to the workstation, and WMS system linkage to achieve ‘unmanned access’.
- Cross-workshop flow: When moulds are moved across regions, the location is tracked in real time through RFID positioning base stations deployed in the factory (Например, UWB positioning system), solving the traditional ’missing moulds” dilemma.
Associates the mould usage data (Например, production batch, processing parameters) with the product quality inspection results, so that the system can automatically locate the moulds when the batch is defective. When the batch is defective, the system automatically locates the problematic moulds and traces the scope of influence.
Quantification of Value: Visible Management Improvement
Efficiency Enhancement: Mould searching time is reduced from 30 minutes to 30 секунд, and the time of changing moulds and adjusting machines is shortened by 40%, which saves labour cost of 50-100 million yuan per annum (calculated on the basis of the scale of 100 sets of moulds).
Cost reduction: downtime is reduced by 30%-50%, misuse loss is reduced by 80%, maintenance cost is reduced by 20%-30%, and mould life is extended by 10%-20%.
Data-driven: real-time mastery of the status of the entire plant mould (in use / техническое обслуживание / idle / scrapped), to support capacity planning, equipment scheduling, accurate decision-making.